2025 Pengarang: Howard Calhoun | [email protected]. Diubah suai terakhir: 2025-01-24 13:22
Pengeluaran tanpa lemak ialah skim khas pengurusan syarikat. Idea utama adalah untuk sentiasa berusaha untuk menghapuskan sebarang jenis kos. Lean manufacturing adalah konsep yang melibatkan penglibatan setiap pekerja dalam prosedur pengoptimuman. Skim sedemikian bertujuan untuk orientasi maksimum terhadap pengguna. Mari kita lihat dengan lebih dekat apa itu sistem pembuatan kurus.
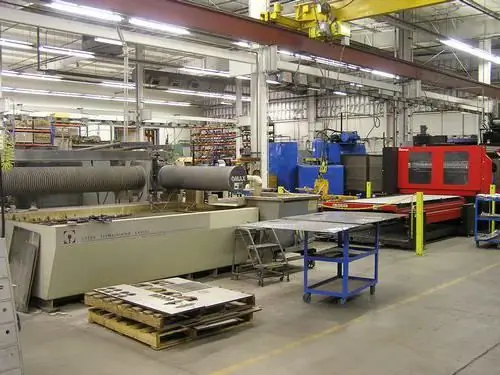
Sejarah kejadian
Pengenalan pembuatan tanpa lemak ke dalam industri berlaku pada tahun 1950-an di Toyota Corporation. Pencipta skim kawalan sedemikian ialah Taiichi Ohno. Sumbangan besar kepada perkembangan lanjut kedua-dua teori dan amalan telah dibuat oleh rakan sejawatnya Shigeo Shingo, yang, antara lain, mencipta kaedah untuk pertukaran pantas. Selepas itu, pakar Amerika menyiasat sistem itu dan mengkonseptualisasikannya di bawah nama pembuatan tanpa lemak (pengeluaran tanpa lemak) - "pengeluaran tanpa lemak". Pada mulanya, konsep ini digunakan terutamanya dalam industri automotif. Selepas beberapa ketika, skema itu disesuaikan dengan prosespengeluaran. Selepas itu, alat pembuatan tanpa lemak mula digunakan dalam penjagaan kesihatan, utiliti, perkhidmatan, perdagangan, ketenteraan, kerajaan dan industri lain.
Sorotan
Pengeluaran kurus di perusahaan melibatkan analisis nilai produk yang dihasilkan untuk pengguna akhir, pada setiap peringkat penciptaan. Objektif utama konsep ini ialah pembentukan proses penghapusan kos yang berterusan. Dalam erti kata lain, pembuatan tanpa lemak ialah penghapusan sebarang aktiviti yang menggunakan sumber tetapi tidak mencipta sebarang nilai untuk pengguna akhir. Sebagai contoh, dia tidak memerlukan produk siap atau komponennya berada dalam stok. Di bawah sistem tradisional, semua kos yang berkaitan dengan perkahwinan, kerja semula, penyimpanan dan kos tidak langsung lain diserahkan kepada pengguna. Pembuatan tanpa lemak ialah satu skim di mana semua aktiviti syarikat dibahagikan kepada proses dan operasi yang menambah dan tidak menambah nilai kepada produk. Oleh itu, tugas utama ialah pengurangan sistematik yang terakhir.
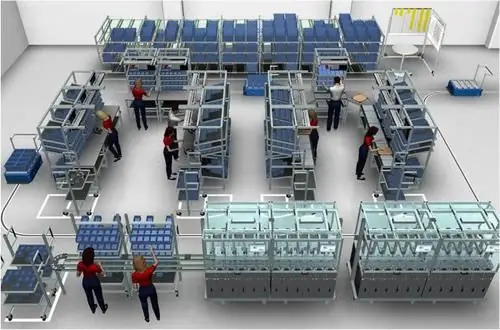
Sisa tanpa lemak
Sebagai sinonim untuk kos, istilah muda kadangkala digunakan. Konsep ini bermaksud pelbagai perbelanjaan, sampah, pembaziran dan sebagainya. Taiichi Ohno mengenal pasti tujuh jenis kos. Kerugian dijana disebabkan oleh:
- tunggu;
- pengeluaran berlebihan;
- penghantaran;
- langkah pemprosesan tambahan;
- pergerakan yang tidak perlu;
- melepaskan barang yang rosak;
- inventori berlebihan.
Jenis kerugian utama Taiichi Ohno dianggap pengeluaran berlebihan. Ia adalah faktor yang menyebabkan kos lain timbul. Item lain telah ditambahkan pada senarai di atas. Jeffrey Liker, seorang penyelidik mengenai pengalaman Toyota, menyebut potensi pekerja yang tidak direalisasikan sebagai satu pembaziran. Punca kos adalah kapasiti terbeban, pekerja apabila menjalankan aktiviti dengan intensiti yang meningkat, serta ketidaksamaan pelaksanaan operasi (contohnya, jadual yang terganggu akibat turun naik dalam permintaan).
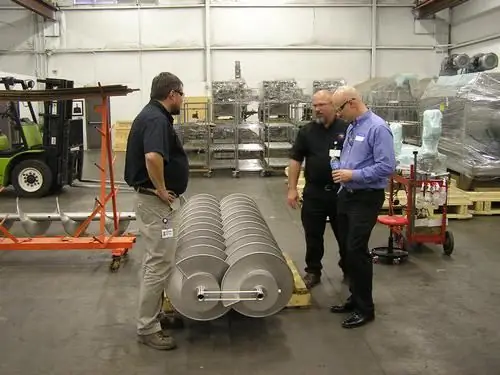
Prinsip
Pengilangan tanpa lemak dibentangkan sebagai proses yang dibahagikan kepada lima peringkat:
- Menentukan nilai produk tertentu.
- Tetapkan aliran nilai produk ini.
- Memastikan aliran berterusan.
- Membolehkan pengguna menarik produk.
- Berusaha untuk kecemerlangan.
Antara prinsip lain yang berasaskan pembuatan tanpa lemak, kami harus menyerlahkan:
- Mencapai kualiti cemerlang - pandangan pertama, sifar kecacatan, mengenal pasti dan menyelesaikan masalah pada peringkat awal.
- Mewujudkan hubungan jangka panjang dengan pengguna melalui perkongsian maklumat, kos dan risiko.
- Fleksibiliti.
Sistem pengeluaran,digunakan dalam Toyota adalah berdasarkan dua prinsip utama: autonomi dan "tepat pada masanya". Yang terakhir ini bermakna bahawa semua elemen yang diperlukan untuk pemasangan tiba di talian tepat pada masa ia diperlukan, dengan ketat dalam kuantiti yang ditentukan untuk proses tertentu untuk mengurangkan stok.
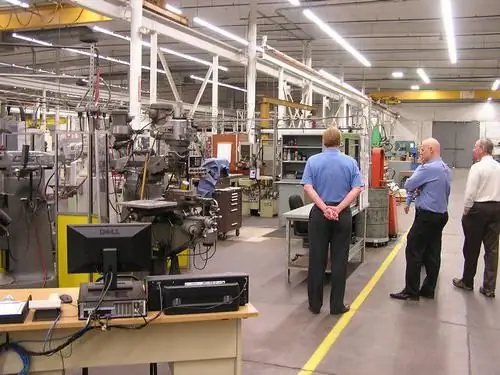
Unsur gubahan
Dalam rangka konsep yang sedang dipertimbangkan, pelbagai komponen dibezakan - kaedah pengeluaran tanpa lemak. Sesetengah daripada mereka mungkin bertindak sebagai skim kawalan. Elemen utama termasuk yang berikut:
- Aliran item tunggal.
- Penjagaan peralatan am.
- Sistem 5S.
- Kaizen.
- Pertukaran pantas.
- Pencegahan kesilapan.
Pilihan Industri
Penjagaan kesihatan kurus ialah konsep untuk mengurangkan masa yang diluangkan oleh kakitangan perubatan yang tidak berkaitan secara langsung dengan membantu orang ramai. Logistik tanpa lemak ialah skim tarikan yang menyatukan semua pembekal yang terlibat dalam aliran nilai. Dalam sistem ini, terdapat penambahan separa rizab dalam jumlah yang kecil. Penunjuk utama dalam skim ini ialah jumlah kos logistik. Alat pembuatan kurus digunakan oleh Pejabat Pos Denmark. Sebagai sebahagian daripada konsep, penyeragaman berskala besar perkhidmatan yang ditawarkan telah dijalankan. Matlamat acara itu adalah untuk meningkatkan produktiviti, mempercepatkan pemindahan. "Kad pembentukan nilai dalam talian" telah diperkenalkanuntuk mengawal dan mengenal pasti perkhidmatan. Juga, sistem motivasi untuk kakitangan jabatan telah dibangunkan dan seterusnya dilaksanakan. Dalam pembinaan, strategi khas telah dibentuk, tertumpu kepada peningkatan kecekapan proses pembinaan pada semua peringkat. Prinsip pembuatan tanpa lemak telah disesuaikan dengan pembangunan perisian. Elemen skim yang dipertimbangkan juga digunakan dalam pentadbiran bandar dan negeri.
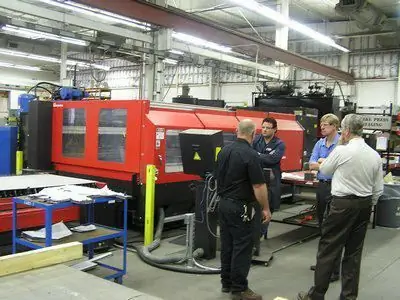
Kaizen
Idea ini telah dirumuskan pada tahun 1950 oleh Dr. Deming. Pengenalan prinsip ini telah membawa keuntungan yang besar kepada syarikat Jepun. Untuk ini, pakar itu dianugerahkan pingat oleh maharaja. Selepas beberapa ketika, Kesatuan Sains dan Teknologi Jepun mengumumkan hadiah kepada mereka. Deming untuk kualiti barangan perkilangan.
Manfaat Falsafah Kaizen
Kebaikan sistem ini telah dinilai dalam setiap sektor perindustrian, di mana keadaan telah diwujudkan untuk memastikan kecekapan dan produktiviti tertinggi. Kaizen dianggap sebagai falsafah Jepun. Ia terdiri daripada menggalakkan perubahan berterusan. Aliran pemikiran kaizen menegaskan bahawa perubahan berterusan adalah satu-satunya jalan menuju kemajuan. Penekanan utama sistem adalah untuk meningkatkan produktiviti dengan menghapuskan kerja yang tidak perlu dan keras. Takrif itu sendiri dicipta dengan menggabungkan dua perkataan: "kai" - "perubahan" ("transformasi"), dan "zen" - "ke arah yang lebih baik." Kelebihan sistem itu cukup jelas menggambarkan kejayaan ekonomi Jepun. Ini diakui bukan sahaja oleh orang Jepun sendiri, tetapi juga oleh pakardamai.
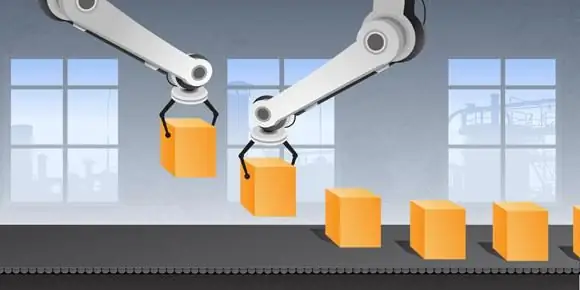
Matlamat Konsep Kaizen
Terdapat lima hala tuju utama di mana pembangunan pengeluaran dijalankan. Ini termasuk:
- Pengurangan sisa.
- Penyelesaian masalah segera.
- Penggunaan optimum.
- Kerja Berpasukan.
- Kualiti terbaik.
Perlu dikatakan bahawa kebanyakan prinsip adalah berdasarkan akal sehat. Komponen utama sistem adalah meningkatkan kualiti barangan, melibatkan setiap pekerja dalam proses, kesediaan untuk interaksi dan perubahan. Semua aktiviti ini tidak memerlukan pengiraan matematik yang rumit atau mencari pendekatan saintifik.
Pengurangan sisa
Prinsip falsafah kaizen bertujuan untuk mengurangkan kerugian dengan ketara pada setiap peringkat (operasi, proses). Salah satu kelebihan utama skim ini ialah ia merangkumi setiap pekerja. Ini, seterusnya, melibatkan pembangunan dan pelaksanaan cadangan penambahbaikan seterusnya di setiap peringkat pengurusan. Kerja sedemikian menyumbang kepada meminimumkan kehilangan sumber.
Penyelesaian masalah segera
Setiap pekerja, mengikut konsep kaizen, mesti mengatasi masalah. Tingkah laku ini menyumbang kepada penyelesaian isu yang cepat. Dengan penyelesaian masalah segera, masa utama tidak meningkat. Penyelesaian masalah segera membolehkan anda mengarahkan aktiviti ke arah yang berkesan.
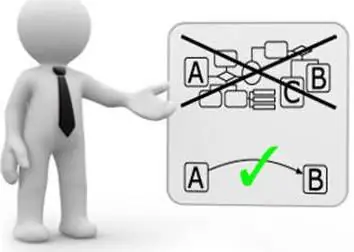
Penggunaan optimum
Sumber dikeluarkan apabila masalah diselesaikan dengan cepat. Mereka boleh digunakan untuk memperbaiki dan mencapai matlamat lain. Bersama-sama, langkah-langkah ini memungkinkan untuk mewujudkan proses pengeluaran yang cekap yang berterusan.
Kerja Berpasukan
Melibatkan semua pekerja dalam menyelesaikan masalah membolehkan anda mencari jalan keluar dengan lebih cepat. Berjaya mengatasi kesukaran menguatkan semangat dan harga diri pekerja syarikat. Kerja berpasukan menghapuskan situasi konflik, menggalakkan pembentukan hubungan kepercayaan antara pekerja yang lebih tinggi dan lebih rendah.
Kualiti terbaik
Penyelesaian masalah yang pantas dan cekap menyumbang kepada kerja berpasukan dan penciptaan sejumlah besar sumber. Ini, seterusnya, akan meningkatkan kualiti produk. Semua ini akan membolehkan syarikat mencapai tahap kapasiti baharu.
Disyorkan:
Pengeluaran minyak motor: ciri, teknologi dan proses pembuatan
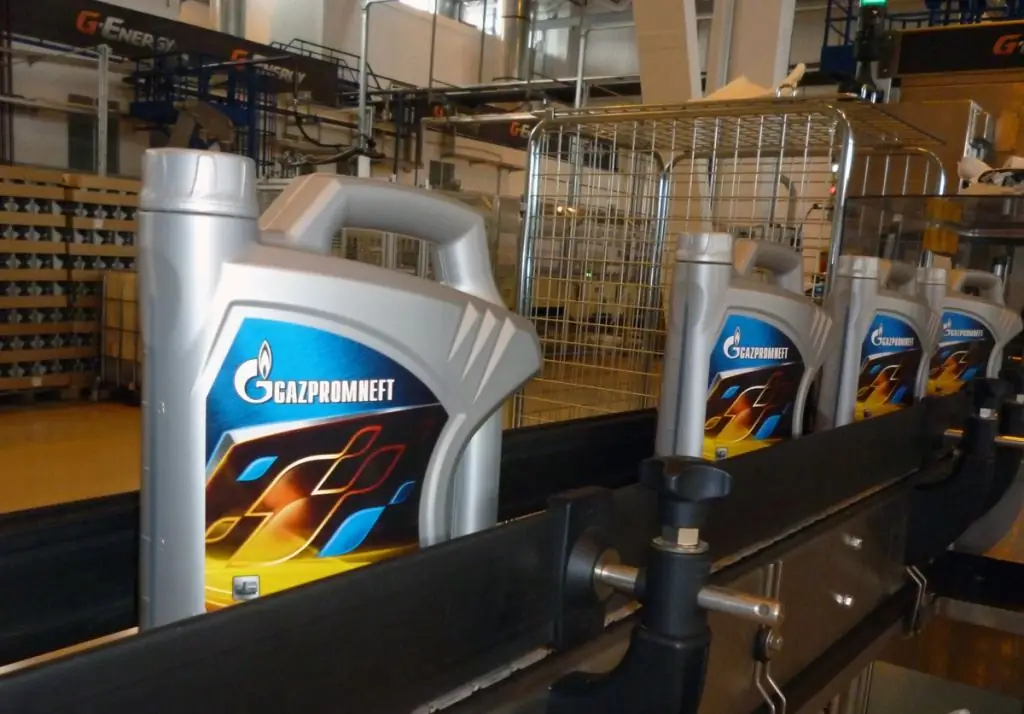
Penghasilan minyak motor, seperti yang lain, tidak lengkap tanpa bahan mentah - bahan dari mana produk akhir diperolehi. Minyak mineral diperbuat daripada petroleum. Tetapi sebelum ia sampai ke loji pelincir, ia perlu melalui beberapa siri pembersihan di kilang penapisan minyak
Pengeluaran moden. Struktur pengeluaran moden. Masalah pengeluaran moden

Industri yang maju dan tahap ekonomi negara yang tinggi adalah faktor utama yang mempengaruhi kekayaan dan kesejahteraan rakyatnya. Negeri sebegini mempunyai peluang dan potensi ekonomi yang besar. Komponen penting ekonomi banyak negara ialah pengeluaran
Pelan perniagaan pengeluaran Styrofoam: langkah demi langkah membuka langkah, teknologi pembuatan, pengiraan pendapatan dan perbelanjaan
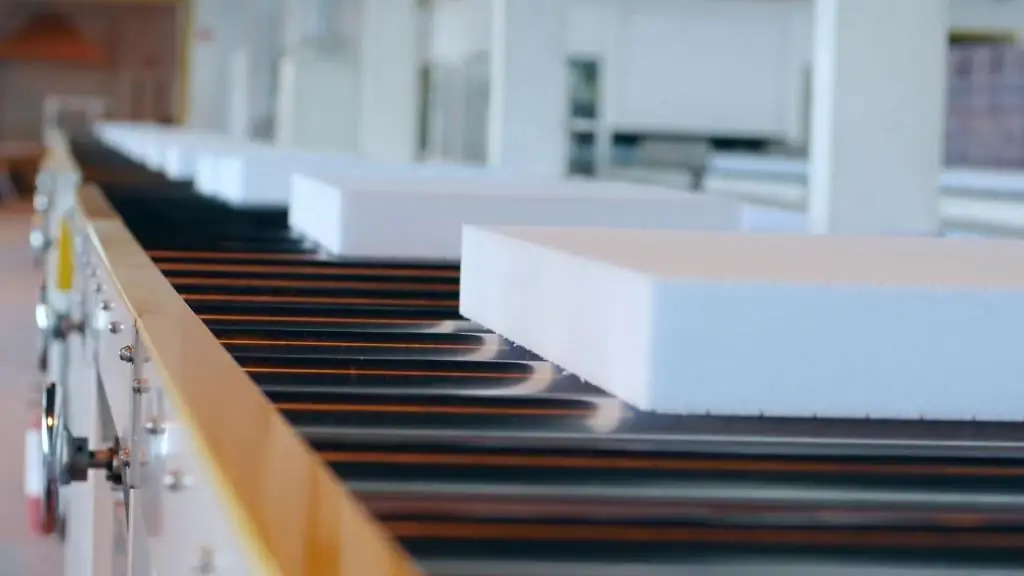
Polyfoam boleh dikaitkan dengan salah satu bahan binaan yang paling banyak digunakan. Permintaan untuknya agak tinggi, kerana terdapat perkembangan pasaran jualan, yang, dengan pendekatan pemasaran yang cekap, boleh memberikan keuntungan yang stabil untuk jangka masa yang panjang. Dalam artikel ini, kami akan mempertimbangkan secara terperinci rancangan perniagaan untuk pengeluaran plastik buih
Pembuatan dan pemasangan struktur logam. Ciri pengeluaran
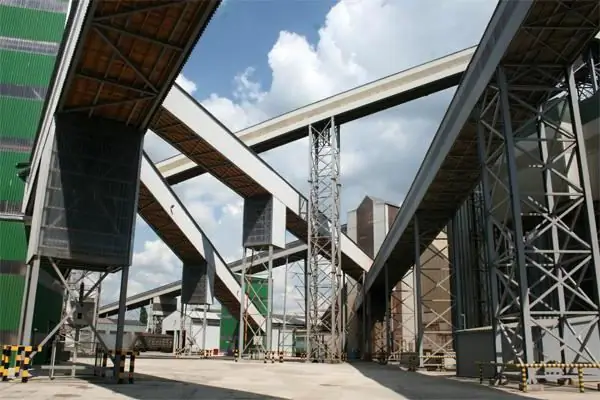
Bangunan pasang siap ialah pilihan terbaik untuk kebanyakan perniagaan, itulah sebabnya kebanyakan pengguna hari ini lebih suka struktur keluli. Pengeluaran, pembuatan dan pemasangan akan dijalankan oleh organisasi pembinaan khas yang menjamin pembinaan berkualiti tinggi untuk sebarang jenis kemudahan
Pengeluaran gas. Kaedah pengeluaran gas. Pengeluaran gas di Rusia
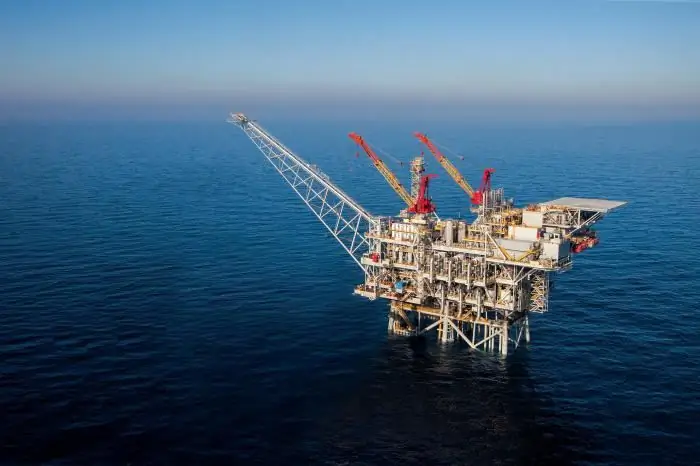
Gas asli terbentuk dengan mencampurkan pelbagai gas dalam kerak bumi. Dalam kebanyakan kes, kedalaman kejadian berkisar antara beberapa ratus meter hingga beberapa kilometer. Perlu diingat bahawa gas boleh terbentuk pada suhu dan tekanan tinggi. Dalam kes ini, tiada akses oksigen ke tempat itu. Sehingga kini, pengeluaran gas telah dilaksanakan dalam beberapa cara, masing-masing akan kita pertimbangkan dalam artikel ini. Tetapi mari kita bercakap tentang segala-galanya dengan teratur